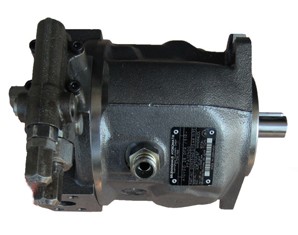
本文按以下3 个方面进行阐述:(1) 正确认识中国液压工业的地位和任务;(2) 成为市场的领导者;(3) 联合是必然趋势。
正确认识中国液压工业的地位和任务回顾改革开放的30 年,我们可以肯定地说中国液压工业的发展成绩喜人。过去的10 年中国液压工业的营业额年年以大幅度增加,平均年增长率达20%。如图1 所示,2007 年中国液压工业的产值达到210 亿,是2000 年的6 倍。预计2008 年将超过250 亿。这还不算没有统计在内的民营液压企业的部分。
中国液压人知道了“得铸造者得液压”的道理。液压铸件有很多特殊的要求, 例如需满足上千万次压力冲击的延伸率要求, 保持液压件清洁度的不粘砂要求,减少油道压力损失的内油道铸造精度要求。能满足上述特别要求的铸造技术在国际上也只有少数的液压件制造公司能掌握。我国的液压工业,特别是民营工业, 如浙江宁波的赛克思液压公司高度重视液压铸造,自己的铸件已在上述的特性上基本能自给,有了良好的基础。近年来液压产品已大量进入国际市场, 华德液压集团每年有几十万台阀出口美国市场, 宁波赛克思液压公司是个400 多人的小厂, 但柱塞泵马达的出口量近1 个亿。我们必须说,中国液压的发展之快,有个重要的原因就是国家经济的快速发展带来了喜人的市场
告诉我们中国过去5 年的GDP 的增长。工业的增长大大地高于GDP 的增长。液压工业紧紧相关的装备制造业、汽车制造装备、塑机、风力发电极大地促进了液压技术的发展。
工程机械行业飞速的发展,振兴了中华,扬了国威,令世人瞩目。中国已经跻身世界工程机械制造大国的行列。她的发展创建了宏大的液压市场。2007 年中国液压市场的容量已跃居世界第三位。然而纵观中国的液压工业, 不得不说我们还挑不起中国市场的大梁。挖掘机的液压件基本上靠国外进口,2007 年中国的挖掘机产量达10 万台,按每台5 个柱塞元件计算,我们就进口了40 万台。重要的工程机械如大型起重机、旋挖钻、路面机械、大型平板车等几乎100%的靠进口液压元件。
德国力士乐一年在中国的营业额超过了40 亿人民币,日本KPM 的营业额则远不止40 亿人民币。2007年我国进口液压件14 亿美元,而国内的液压产值仅为210 亿人民币。中国工程机械行业利润的70%被进口件吃掉,进口液压元件已占了整机成本的40%。不仅如此, 虽然中国工程机械产品的技术竞争力还很薄弱,但产品出口总量却很大,这引起了境外同行企业的联合封杀。目前我国工程机械行业主要进口的基础零部件包括液压元器件、发动机、控制元器件、传动系统等。尤其是液压元器件,特殊钢材的国外供应商企业依靠市场垄断地位,制订“霸王条款”。一些国际大型零部件生产商还联合起来给中国企业设计同规格尺寸的零部件,让中国的出口产品在同质上进行竞争。跨国零部件生产商在中国生产的一些产品甚至是欧美发达国家已经淘汰的产品。但即便如此,中国企业也并非轻易就能买得到。当前如何按照党中央的部署走自主开发之路,创造有我们自己知识产权的产品,主机厂家正在快马加鞭地进行。然而主机厂近年来碰到了电子液压供应商供货周期的制约,资源的紧张已经让主机厂家不得不把更多的精力放到了解决“交货期”的问题上,不得不修改自己的发展计划,放慢我们的发展步伐。世界知名的供货商满足不了中国主机厂家的需求,一而再、再而三地延长交货期。这引起了国家相关部门、企业家的思考:仅仅是货源紧张,还是变相制裁?已经没有再讨论价格的余地,主机如何在价格上与世界名牌企业平等竞争?货源都解决不了,如何再提自主创新?中国的基础件行业为什么如此不争气?国际权威市场分析表明2011 年世界工程机械市场为1310 亿美元,中国将占31%,即406 亿美元,2842亿人民币。如何满足他们对液压元件的需求?
当前出现的世界金融风暴,让我们更清醒地认识到掌握核心技术的重要性。著名经济学家吴敬琏说:“我们掉进了美元的陷阱! ”基础件工业差,主机大幅度出口,掉进陷阱是必然的。我们在辛辛苦苦地养活美国。我们还没有年营业额超过10 个亿的液压厂家,主机厂不得不依赖外国厂家,受他们各种制约。制造业按其自制比例的多少可分为上游、中游和下游,越往上游,越难。零部件是制造业的上游,液压是制造业的中游,主机是制造业的下游。主机在下游,莺歌燕舞,一派繁荣;处于它上游的液压工业步履艰难,承受着来自它下游和上游两方面的压力。这是因为它投资大、见效慢。“我们出口的是血汗,进口的是眼泪! ”中国液压气动密封件工业协会沙宝森理事长精辟地描述了这一形势。中国市场极具吸引力,除了欧美和日本厂商,俄罗斯也来了。中国的液压工业不能再等待, 中国的液压工业必须振兴。
成为市场的领导者
面对这样严峻的形势我们该怎么办呢?首先让我们来分析一下,我们为什么会落后。20 世纪70~80 年代: 我们产品落后,生产手段落后;20 世纪90年代:我们体制落后,管理落后;21世纪的现在:我们理念落后,市场能力落后。我自身经历了中国液压发展的历程:1978 以前:在原苏联液压技术的基础上,开始了自己的液压工业。压力低、品种少“走起来一条线,停下来一大片”的质量和技术水平束缚了中国机械制造业的发展。1978~1998年:大量引进德国、美国和日本液压技术。体制落后,引进的技术没有能很好的发挥,但市场活跃了,促进了中国制造业发展。“有问题找力士乐”,主机开始高速发展,进入世界行列。1998~2008 年:主机高速发展,大量采用国外知名厂家的产品,得到的不仅是产品,还有系统和应用技术。外国公司从技术进入、市场进入,转而资本进入。中国的液压工业变成了配角。“中国液压就像中国足球”。2008 至今:外国公司以拖延交货的形式制约主机发展,形成了各家千篇一律的液压系统,使“发展中国自主知识产权产品”几乎成为空话。液压工业“出口的是血汗,进口的是眼泪”。发展民族液压工业已迫在眉睫。理念落后,市场能力落后,表现在什么地方呢?
(1) 注重产品发展,不注意将产品变为商品!
(2) 注重营业额的增加,不注意产品的流向!
(3) 注重对名牌产品的简单追逐,不注意按应用开发产品!
(4) 注重液压的发展,不注意电液结合!
(5) 注重以出厂为基点的产品质量控制,不注意以使用为基点的质量管理!
(6) 注重务实,将自己定位在“廉价”,不注意宏观的目标,打造成合格的供应商!几乎没有年营业额超过10 亿元的厂家,规模小不利于竞争!如何成为市场的领导者?
2.1 开发出国家级的液压产品
要成为市场的领导者必须解决的第一件事就是满足市场需求的产品。这是个“先有鸡还是先有蛋”的问题。目前我们的液压产品大部分是仿制的,而且仿制的是20 世纪80、90 年代的产品。以柱塞泵为例主要是仿制力士乐的A7V、A4VSO、A10VSO、A11VO 和日本的K3V。性能上落后于人家20、30 年;产品的质量不能和人家原装的比,产量最大的厂家也仅有3 万台,无法和人家年产100 万台的外国厂家去竞争。如此谈什么市场的领导者、凭什么让人家主机厂选用你的产品? 主机不选用,我们又如何发展?开发出“国家级”的产品至关重要,有了国家级的产品主机厂就敢选用,因为生产的厂家多;有了国家级的产品就能把目前液压行业厂家小而散的状况改变,完全可以与国外公司竞争。目前我们的液压工业队伍中有资深的液压元件专家,有大专院校的先进虚拟设计手段,有具备几十年液压元件中关键零件加工的工艺专家, 他们不仅熟知工艺关键甚至熟知目前国际上最新的工艺手段。应该说开发我们的国家级产品不应该成问题, 但我们缺乏有足够力量的组织者。在国家资金支持下, 走联合开发的路子是可行的办法。振兴中国液压工业,国家应从产品开发入手,利用现在的中国液压气动密封件工业协会,集中全国的有关力量迅速开发我们国家级的产品。从生产能力入手的“技术改造”会出现低档产品的生产扩大,只能延续我们是液压大国而不能成为液压强国的现状。
2.2 认清技术发展趋势
认清电子控制的重要性现在驱动和控制技术向DCC 即分散式控制系统发展。认清电子控制的重要性,我们就不需要追求大而全的发展方向,因为系统是靠电子集成的,系统不再依赖液压元件的“Total Solution”。每个厂家把自己的拿手产品做好、做精、做可靠,主机厂会自行成套。我们需要建立液压电子控制的专业队伍,中国液压气动密封件工业协会应该建立电子控制分会。
联合是必然趋势
大家都说中国的液压就像中国的足球。同是体育运动,为什么乒乓球可以称霸世界而足球在亚洲都是弱旅? 液压要发展恐怕联合是必然趋势。我们是市场经济,不能强制企业的联合和重组,但可以实施引导,推进联合。首先我们应该考虑联合的目的,不能为了联合而联合。联合也是多方面的,如:
(1) 液压制造商的团结协作;
(2) 主机厂与元件供应商的团结协作;
(3) 工业协会和厂家的协作;
(4) 液压制造商与上游工业的团结协作;
(5) 液压制造商与大学的团结协作。
联合不是哥们义气, 联合不能是政治上的一时冲动之举。联合必须遵守市场规律。决不能干3 个和尚没水喝的事。联合必须以有利于市场发展为前提,应该考虑:联合的集团公司应有利于创建国家级的液压产品。联合的集团公司:能让主机厂有信心;能让主机厂得到全套的所需液压元件;能造势,主机厂的产品更容易在世界市场销售;能与国际大公司抗衡,让主机厂脱离外国供应商的制裁;生产批量大,成本将降低,使主机厂产品更有价格优势。